Optimizing RTO Thermal Destruction with FLEXERAMIC® Ceramic Media
Published on: October 28, 2024 Topics: FLEXERAMIC ®, Mass Transfer MediaHow would your company withstand the impact of a $33 million fine? That would be the amount in today’s dollars (adjusting for inflation) of the $25 million fine against Tonawanda Coke Corporation in New York in 2013 for violating the Clean Air Act and Resource Conservation and Recovery Act. The company’s coke ovens were releasing benzene, a known carcinogen, into the surrounding community — a carcinogen that poses significant health risks. Inadequate pollution control measures caused the violations, leading to substantial financial penalties and a four-year shutdown.
What is thermal destruction?
Thermal destruction is a widely employed technique for eliminating hazardous air pollutants (HAPs) and volatile organic compounds (VOCs), including known carcinogens, from industrial exhaust streams. This process involves subjecting the polluted air to extremely high temperatures, typically ranging from 1400°F to 1600°F (760°C to 870°C). These temperatures allow for nearly complete combustion and conversion of these pollutants into stable byproducts such as water vapor and carbon dioxide.
Regenerative Thermal Oxidizers (RTOs) are specialized systems designed to achieve thermal destruction while maximizing energy efficiency. RTOs utilize a regenerative heat exchange process by transferring heat to and from a ceramic media bed.
As the airflow direction is periodically reversed, the heated ceramic media transfers its stored thermal energy to preheat the incoming, polluted airstream before it enters the combustion chamber. This preheating minimizes the amount of supplemental fuel required to reach the desired oxidation temperatures for destroying VOCs and HAPs. The clean air stream is then pushed through the cooler ceramic bed, recovering the heat for use in the next cycle.
The ceramic media installed within the tower is a critical part of the RTO design. The ceramic media’s ability to rapidly cycle between absorbing and releasing heat is essential for the RTO system’s continuous operation and energy efficiency. Properties like high thermal stability, heat transfer rate and resistance to thermal shock make specialized Structured RTO media well-suited for this demanding heat recovery application.
What is the thermal efficiency of an RTO? Achieving optimized usage of an RTO
While thermal destruction is an effective means of air pollution control, it presents several challenges. First, the high temperatures required for complete oxidation can result in significant energy consumption and operational costs. Also, exhaust gases often contain corrosive compounds that can degrade conventional heat transfer media over time, reducing efficiency and increasing maintenance requirements.
Moreover, certain industries must adhere to stringent regulations and standards, requiring a highly efficient and reliable thermal destruction system. One example is the chemical processing sector, where improper handling or destruction of HAPs can pose severe risks to human health and the environment, potentially leading to hefty fines and legal consequences.
Efficient thermal destruction relies on an engineered RTO tower design and the proper ceramic media selection that allows for proper heat retention while maintaining airflow volume —without burning excess energy or unduly stressing associated equipment. A well-designed tower maximizes heat recovery while minimizing the energy required to maintain the necessary operating temperature for oxidation reactions. With the right type of media placed according to the engineered design, an RTO unit can provide 98% or better VOC destruction efficiencies and 99% or better destruction of hazardous air pollutants (HAPs). Knight Material Technologies has decades of experience designing RTO media beds and identifying the proper mix of random and structured media to achieve this balance.
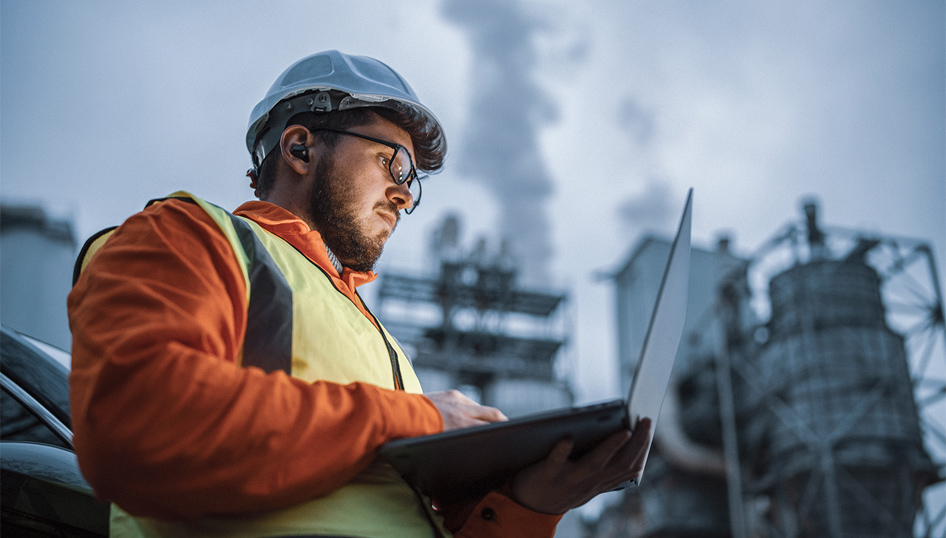
The criticality of structured ceramic media
Recognizing the challenges associated with thermal destruction, Knight Material Technologies has developed FLEXERAMIC® advanced ceramic heat transfer media. The FLEXERAMIC® type 28 is structured media specifically designed for use in RTOs and other high-temperature applications. This unique ceramic structured packing design, vastly different than monolithic ceramic blocks, offers several key advantages:
- High thermal stability and optimized heat transfer: Manufactured using advanced ceramic materials, FLEXERAMIC® exhibits exceptional thermal stability, enabling it to withstand the extreme temperatures encountered in RTO combustion chambers while maintaining its structural integrity and performance over extended periods. FLEXERAMIC’s structured packing configuration with corrugated openings gives it a high surface area and allows free airflow compared to monolithic blocks. This enhanced heat transfer capability facilitates rapid thermal regeneration during the RTO cycle, maximizing energy and pollutant destruction efficiency.
- Fouling Prevention and Uniform Gas Distribution: The amount and time frame for fouling differs depending on the process and VOCs involved. The uniquely designed airflow passages in the FLEXERAMIC ceramic media facilitate the free flow of gases through the media as fouling occurs, mitigating potential plugging and restricted airflow that can impede proper RTO functioning and energy consumption. The uniform gas distribution also minimizes channeling and hot spots, promoting thorough mixing to ensure complete oxidation of VOCs and HAPs.
-
Low pressure drop: The optimized design of FLEXERAMIC minimizes pressure drop across the RTO system, optimizing airflow and reducing energy consumption associated with fan power requirements.
Benefits of structured media in RTOs
The biggest benefits of effective thermal destruction systems like RTOs equipped with advanced ceramic media such as FLEXERAMIC include:
- Compliance with environmental regulations: Thermal destruction is a proven technology for meeting stringent air pollution control standards set by regulatory bodies like the Environmental Protection Agency (EPA) and local air quality management districts. Companies can avoid costly fines and penalties associated with non-compliance by achieving high destruction efficiencies for HAPs and VOCs.
- Avoiding production shutdowns: In many industries, failure to comply with emissions regulations can result in temporary or permanent shutdown of operations, leading to significant financial losses and disruptions. Implementing reliable and efficient thermal destruction systems helps companies maintain continuous production while meeting environmental standards, preventing costly shutdowns.
- Mitigating environmental and health risks: Improper handling or release of HAPs and VOCs can pose severe environmental, air quality, and human health risks. Thermal destruction effectively neutralizes these pollutants, minimizing the potential for environmental contamination, legal liabilities, and public health concerns.
By leveraging the advanced capabilities of FLEXERAMIC, industries can achieve effective and efficient thermal destruction of hazardous air pollutants while minimizing operational costs and ensuring compliance with environmental regulations.
As industries prioritize air pollution control and strive for sustainable operations, the demand for high-performance thermal destruction systems will only increase. FLEXERAMIC ceramic media from Knight Material Technologies offers a compelling solution, combining exceptional thermal stability, optimized heat transfer, uniform gas distribution, chemical resistance and low pressure drop characteristics. By integrating FLEXERAMIC into the RTO, industries can optimize thermal destruction processes, reduce energy consumption and minimize maintenance requirements to reduce energy costs and meet environmental standards.
For more information on selecting the right ceramic media for your RTO, visit our website or contact us to speak with one of our application engineers.