Save on Energy Costs by Optimizing RTO Thermal Efficiencies
Published on: June 23, 2023 Topics: RTOHeat transfer packing selection could be the key
What is escaping from your regenerative oxidizing tower (RTO)? Wasted energy could release profits while you strive to capture volatile organic compounds (VOCs). A variety of factors can impact the thermal efficiency of your RTO.
The choice of RTO packing material for the ceramic bed can play a critical role in optimizing thermal efficiencies. Optimizing thermal efficiencies directly correlates to energy savings—your choice of ceramic media matters.
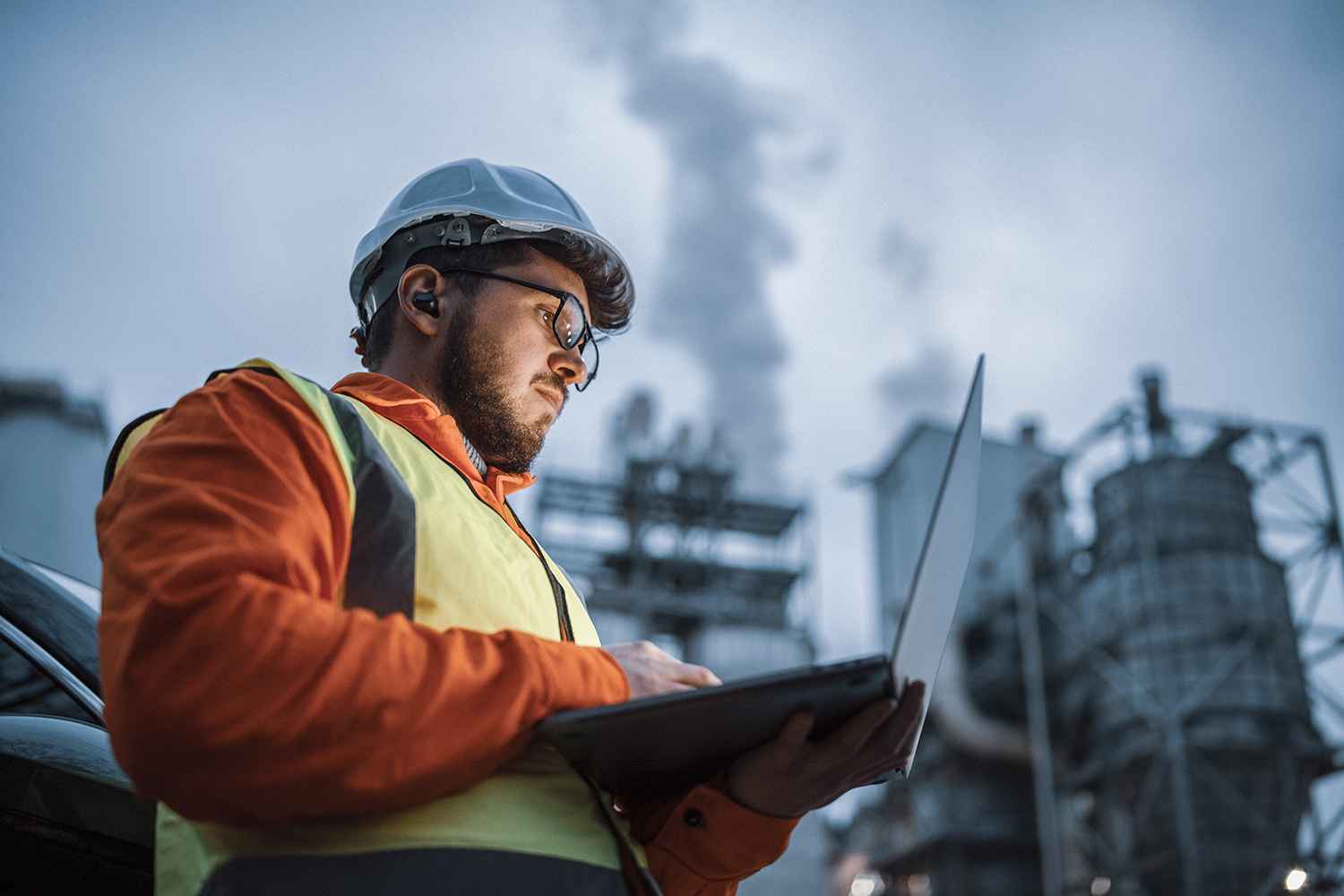
What is an RTO?
A regenerative thermal oxidizer (RTO) is a type of air pollution control equipment that is commonly used to treat industrial exhaust gases by oxidizing them at high temperatures. This breaks down the VOCs into harmless byproducts like water and carbon dioxide.
During its operation, the exhaust gas is directed through ceramic RTO heat exchange media heated by a burner system. The hot exhaust gas combusts the incoming pollutants.
While this type of combustion device averages thermal energy recovery of approximately 95%, to achieve its intended purpose, the thermal oxidizer requires a significant amount of energy. This is due to the high temperatures required in the combustion chamber to oxidize the VOCs. Temperatures can reach up to 1700° F or higher, requiring substantial amounts of natural gas and electricity.
The ceramic media captures and retains this heat, transferring it to the incoming exhaust gas in the next cycle. Two key factors work to optimize RTO operation’s thermal efficiencies and energy expenditure: gas distribution and particulate matter.
Enhanced gas distribution to increase RTO efficiency
In a thermal system, gas distribution can significantly impact thermal energy. RTO thermal efficiency is a measure of the amount of heat energy that is converted into useful work or output relative to the total amount of heat energy supplied to the system.
The distribution of gas refers to how the fuel and air are mixed and distributed within the system’s combustion chamber. The combustion process relies on a mixture of fuel and air in the correct proportions. If the distribution of gas is not optimal, it can lead to incomplete combustion, which results in lower RTO thermal efficiency.
The following are some of the effects of gas distribution on thermal efficiency:
- Complete Combustion: Fuel and air must be mixed in the correct proportion to ensure complete combustion for maximum thermal efficiency. This means that all the fuel is burned with enough oxygen, which results in maximum heat energy output.
- Combustion Stability: Gas distribution impacts combustion process stability. When the gas is not evenly distributed, this can result in an uneven combustion process, reducing the system’s thermal efficiency.
- Flame Temperature: Gas distribution can also affect the temperature of the flame in the combustion chamber. A higher flame temperature generally leads to higher thermal efficiency, generating more heat energy.
- Emissions: Incomplete combustion due to poor gas distribution can result in higher levels of emissions, reducing thermal efficiencies and increasing the environmental impact. Consequences can include fines or even an unscheduled shutdown.
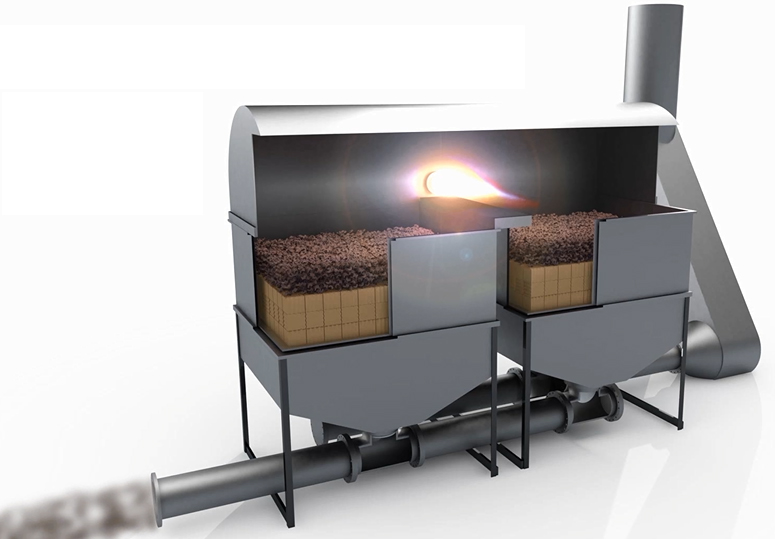
The right heat transfer packing will save energy costs.
Particulate matter, emissions and thermal efficiencies
The type and quantity of pollutants generated during processing can impact the performance and effectiveness of the RTO, particularly in relation to the type of ceramic media packing the tower.
For example, suppose the process generates high levels of particulate matter over time. In that case, this can increase the risk of clogging or fouling a monolithic small cell design, reducing its efficiency and impacting the proper capture of emissions.
The thermal efficiency of an RTO can directly impact the emissions, a significant financial consideration for operators. An RTO oxidizes pollutants in the exhaust gas at high temperatures.
The greater the thermal efficiency of the RTO, the more it can help reduce emissions of hazardous air pollutants (HAPS) that might be generated during the combustion process. For example, incomplete combustion can form nitrogen oxides (NOx), a greenhouse gas and major air pollutant. A more efficient RTO can reduce the formation of NOx by ensuring pollutants are thoroughly combusted. This efficiency also uses less energy.
VOCs are deemed harmful pollutants, and their emission is regulated by the Environmental Protection Agency (EPA) through the Clean Air Act. State and local agencies impose their own regulations and enforcement programs.
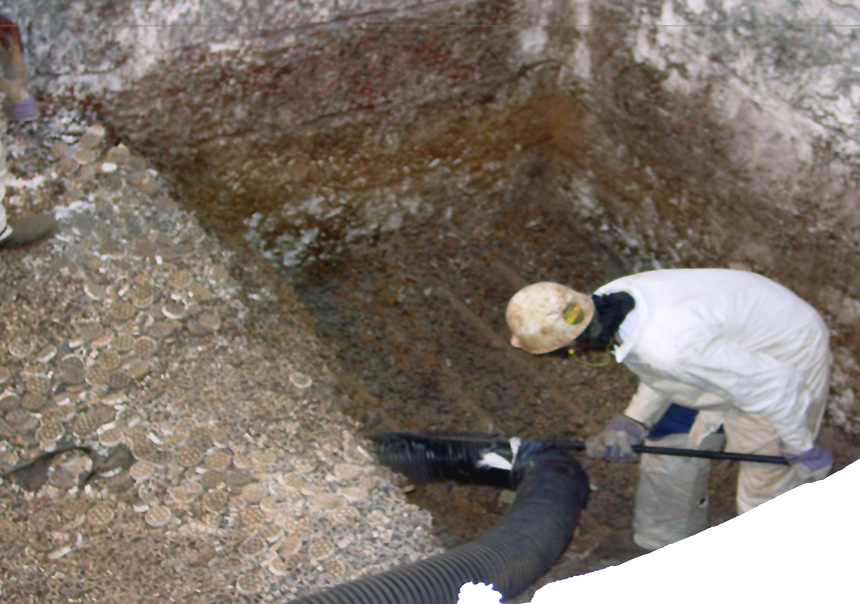
The wrong heat transfer packing could result in significant plugging and extended downtime.
RTO design and ceramic media choice
Three basic choices for the heat transfer ceramic media used in the RTO design are random packing, monolithic small cells, or geometric structured media blocks. A long-term view of these media types, particularly focusing on the differences between the monolithic or geometric blocks, points out the energy savings or losses associated with each.
Newly installed media exhibits a significant tradeoff between thermal efficiency and pressure drop. Over time, and after millions of cubic feet of gas pass through the RTO, gas distribution and particulate retention play major roles in continued thermal efficiency performance and the lifespan of the heat transfer media bed.
Initially, a small cell monolithic media will have very low pressure drop and high thermal efficiency. Its continued performance, however, depends greatly on the particulates present in the inlet gas, either from normal operations or during an upset condition. Over time, the cells can quickly become plugged, creating a “cold face” or blocked area. This plugged-up area no longer performs its function and detracts from overall system efficiency. This creates:
- Area with no airflow
- Increased velocity in the rest of the bed
- Large pressure drop increase
- Loss of heat recovery
- Higher energy draw
On the other hand, a geometric waveform patterned ceramic media such as FLEXERAMIC® structured packing allows for more even distribution of the liquid or gas flow through the tower.
Less resistance means a lower pressure drop, requiring less energy to move the gas through the tower.
The waveform pattern also increases the surface area. Maximizing surface area increases contact with the gas flow, increasing the efficiency of the distillation process. This increased RTO energy efficiency means less energy is required to break down the VOCs.
In case an area is cold face plugged, a mixed media bed that utilizes FLEXERAMIC® structured packing supplies:
- Air movement around the plugged area
- Small pressure drop increase
- Small loss of heat recovery
- Burnout more effective on plugged area
- Greater thermal efficiencies
Conclusion
Geometric ceramic structured packing is a highly effective tower packing material that can help companies save on energy costs—up to 35% in some cases. By reducing pressure drop and maximizing surface area, geometric structured packing such as FLEXERAMIC structured packing allows for a more efficient distillation process, resulting in significant energy savings.
Give us a call to discuss your RTO tower design or upgrade. Our engineers can design and recommend the right mix of structured and random media packing to resolve your RTO challenges, improve operating costs by sparing energy usage, or resolve pressure drop, particulate accumulation, etc.