Understanding the Difference between Modified PTFE and PFA Linings
Published on: July 8, 2025 Topics: LiningsAdvanced Protection for Your Process Equipment
No facility benefits from unplanned downtime; this is a universal truth across manufacturing. However, the consequences and costs of downtime are currently at their highest levels ever, according to recent research. A study published this year reveals that UK and European manufacturers alone are projected to lose more than $103 billion (£80 billion) in 2025 due to unplanned downtime, with chemical processing facilities facing costs of 400-600 hours annually, and individual incidents could reach $260,000 per hour.
In chemical plants, the impact extends beyond immediate financial losses to include equipment replacement costs, regulatory compliance issues and potential personnel safety concerns. One way to avoid downtime is to implement proper corrosion protection through the selection of suitable materials. This can optimize equipment lifespan, reducing maintenance and providing the best return on investment (ROI) for plant equipment costs.
Fluoropolymer linings have been the industry standard for decades, with both modified PTFE and PFA offering excellent chemical resistance across a wide range of applications. Understanding the specific advantages of each can help you select the optimal solution for your process requirements. Electro Chemical Manufacturing (ECM) utilizes both modified PTFE and PFA for equipment lining, helping to select the right one to protect your process.
What is the difference between modified PTFE and PFA?
Modified PTFE is an enhanced version of traditional polytetrafluoroethylene that incorporates a small amount (less than 1%) of a perfluorinated modifier into its molecular structure to overcome fabrication and performance limitations of standard PTFE. The key improvements include superior weldability, which makes it much easier to fabricate and install compared to traditional PTFE, and a denser molecular structure with reduced void space, resulting in significantly lower chemical permeation rates. These enhancements make modified PTFE particularly valuable for chemical processing applications where both fabrication efficiency and long-term chemical resistance are critical.
PFA (perfluoro alkoxy) is a melt-processable fluoropolymer that combines the exceptional chemical resistance and non-stick properties of PTFE with the ability to be processed using conventional thermoplastic techniques like injection molding and extrusion. Unlike PTFE, PFA can be welded, thermoformed and fabricated at elevated temperatures while maintaining its chemical inertness and mechanical properties, making it ideal for complex shapes and precision components in demanding chemical processing environments.
The global chemical processing industry today
The global chemical processing industry, valued at more than $5.72 trillion U.S. dollars in 2022, faces significant challenges from corrosion. Even without a worst-case scenario, corrosion leads to increased material utilization, higher energy consumption, production losses, potential environmental damage and greater greenhouse gas emissions due to inefficiencies and maintenance needs.
Chemical vessels and pipes require superior protection against acids, bases and other aggressive substances. It is essential to select the optimal material for your specific corrosion prevention application. As a solutions provider with expertise across the full spectrum of fluoropolymer technologies, Electro Chemical Manufacturing, part of the Knight Material Technologies family, can help you determine which material will deliver the best performance and value for your specific requirements. We work with many different materials, including modified PTFE, PVDF, ECTFE, CTFE, ETFE and PFA, matching the material to the desired performance specifications.
PFA key advantages: Technical properties and performance
PFA represents an evolution within the fluoropolymer technology space. It was first developed in the 1970s to complement the established performance of polytetrafluoroethylene (PTFE), which has been trusted in industry since its invention in 1938. Both materials offer exceptional protection against chemical corrosion and interaction with oxidizing acids, organic solvents, inorganic bases, mineral acids and strong alkalis.
When properly applied as a lining solution, PFA creates an exceptionally robust barrier between aggressive chemicals and the metal surface of pipes and other critical equipment used in chemical processing facilities.
PFA’s molecular structure provides exceptional resistance to virtually all industrial chemicals while offering improved processability compared to PTFE. PFA can be formed, extruded and welded, which is preferable for use in complex shapes. This unique combination delivers key benefits:
- Exceptional chemical resistance across the pH spectrum
- Superior temperature cycling resistance
- Enhanced uniformity and consistency in liner production
- Smoother, uniform surface finish that reduces contamination and build-up
Understanding permeation in fluoropolymer linings
Permeation performance is a critical factor when selecting fluoropolymer linings for corrosion-resistant applications. Permeation—the molecular transport of chemicals through a polymer—occurs in any polymer/fluid interaction and is driven by concentration or pressure gradients. This process can impact the long-term performance and reliability of protective linings.
The primary issue is material weldability, as most failures or problems typically occur in the weld area. For example, PTFE and modified PTFE do not melt, requiring a different material welded to these substances to form the weld seam. The strongest weld is achieved when matching PFA to PFA, resulting in a weld that maintains good chemical resistance over a wide range of operating temperatures and various chemistries. When a weld seam fails, multiple problems might occur, including:
- Corrosion of the steel substrate behind the polymer liner
- Pressure build-up between the liner and substrate
- Blister formation due to condensation inside the polymer liner
- Liner deformation during thermal cycling
- Fugitive emissions and leaks
When operations handle ultra-pure chemicals, PFA is almost universally chemically resistant. For example, it is inherently UV stable without requiring additives. Therefore, PFA will not leach out or react with other substances. This enhanced stability helps maintain a more consistent production and reduces the risk of contamination or premature failures, making it particularly well-suited for these demanding applications. In addition, its smooth surface is especially important in the semiconductor, pharmaceutical and food industries.
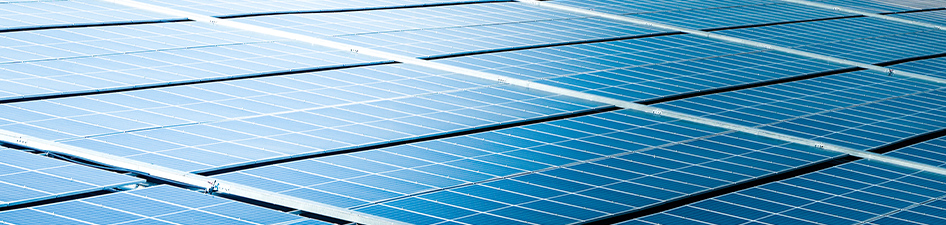
Value considerations: Initial cost vs. long-term performance
While PFA typically has a higher initial cost than modified PTFE, many operations find that its performance advantages can deliver greater long-term value or return on the initial investment. When evaluating corrosion protection options, keep in mind:
- Total lifecycle costs including installation, maintenance, and expected service life
- The operational impact of potential failures or unplanned downtime
- Process-specific requirements that may benefit from PFA’s enhanced performance characteristics
For many critical applications, the potential for extended service life and reduced maintenance with PFA can offset the higher initial investment. However, for applications where modified PTFE’s performance meets all requirements, it continues to offer excellent value.
Manufacturing and application differences between modified PTFE and PFA
While both modified PTFE and PFA provide excellent chemical resistance, PFA’s melt-processable nature creates several manufacturing advantages that can benefit certain applications:
-
Fabrication Process
PFA can be extruded into sheets with a glass fabric backing that is partially embedded during the extrusion process. This results in mechanically locked backing that provides superior bonding with adhesives.
Unlike PTFE’s sintering process, which can result in varied fusion quality and potential microporosity, PFA’s manufacturing process creates more consistent material properties throughout the lining. This uniformity translates to more reliable protection and predictable performance in service.
-
Weldability
When creating PFA-to-PFA welds, both the sheet material and the weld rod are heated to a melting state. This allows the molecular “chains” to intertwine and mingle before cooling down and solidifying. This process creates exceptional bonding at the molecular level. PFA-to-PFA welds are therefore typically stronger than a PFA to a modified PTFE or PTFE weld.
Enhanced weldability is critical for fabricating complex shapes with fewer potential failure points and for creating reliable seams in lined equipment. For customers, this translates directly to longer service life and improved reliability, as welds are typically the most vulnerable areas in fluoropolymer-lined equipment.
Developing your corrosion protection strategy
ECM offers complete engineered solutions for critical corrosion protection using high-performance materials specifically designed for corrosive and high-temperature environments in industrial applications. Our materials engineering experts bring decades of experience working with the full spectrum of fluoropolymer technologies, including both PFA and modified PTFE. We take a consultative approach to understand your specific requirements and recommend the optimal material for your application, whether that’s PFA, modified PTFE or another fluoropolymer option.
Our membership in the Materials Technology Institute keeps us at the forefront of fluoropolymer application technology, ensuring you receive the most current recommendations for your equipment. ECM’s engineers can evaluate your specific processes to recommend the optimal lining material for your unique requirements, considering factors such as chemical compatibility, temperature ranges, mechanical stresses and budget constraints.
Take action today
Contact ECM today to discuss how our PFA solutions can address your specific corrosion protection challenges. Our team will:
- Evaluate your current processing conditions
- Evaluate your current process requirements and identify the optimal fluoropolymer solution for your specific application
- Recommend customized PFA or modified PTFE solutions for your most demanding applications
- Provide a comprehensive cost-benefit analysis demonstrating long-term ROI
Do not risk equipment failure or product contamination with inferior lining materials. Let ECM’s expert team help you develop a comprehensive corrosion protection strategy, evaluating these factors based on your specific process conditions to determine the most cost-effective solution.