Teflon™ PFA – The Chemical Resistance King of Fluoropolymer Linings
Published on: October 17, 2023 Topics: LiningsWhen you talk about fluoropolymer lining protection against chemical corrosion and permeation, PFA (perfluoroalkoxy) delivers the highest level of resistance. We can thank the strength of the Fluorine-Carbon bond within the PFA polymer chain for its incredible inertness. These bonds are so tight and enduring that they simply do not allow other atoms or molecules to separate them. This makes PFA the strongest of the fluoropolymers for preventing chemical corrosion, permeation and reaction.
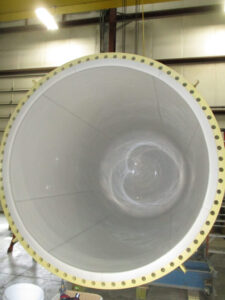
Teflon PFA Lined Chemical Process Vessel
You may already know of PFA by a famous brand name – Teflon™. That’s the identity trademarked by The Chemours Company for its line of three fully fluorinated fluoropolymers – Teflon™ PFA, Teflon™ FEP, and Teflon™ PTFE. Though each is “fully fluorinated,” their chemistries do vary, and they each have slightly different performance parameters. In this article, we’ll discuss their PFA product.
Several companies polymerize PFA resins. For instance, Daikin Industries makes Neoflon™ and Hyflon® is the branded PFA of Solvay Solexis. Regardless of its manufacturer, rest assured that Electro Chemical Manufacturing (ECM) thoroughly understands PFA and its performance characteristics.
Now that identity is clear and Teflon™ PFA is our focus, let’s talk about what it’s used for and why.
When to use PFA
Teflon™ PFA is very effective against the chemical corrosion, permeation, and interaction of oxidizing acids, organic solvents, inorganic bases, mineral acids and strong alkalis – pretty much all types of corrosive chemicals.
PFA also has a superior high temperature service limit of 180°C (260°F) and can withstand severe temperature cycling conditions (going back and forth between cold and hot repeatedly) quite well. As FYI, the PFA resin itself can tolerate higher temperatures. However, the adhesive used to apply PFA as a lining cannot, and so the upper temperature service limit reflects this.
And because of PFA’s chemical inertness and the fact it does not leach impurities into your system, it is ideal for applications where ultra high purity levels are required.
Despite its extraordinary protective power, there are still some situations where PFA would not be recommended. For instance, PFA does not tolerate physical interaction well – i.e. abrasion. If you are managing a slurry or a mixture with larger particulates, you’ll likely be better served by another fluoropolymer.
Industries that benefit from PFAs
Here are a few industries that enjoy the protective power of Teflon™ PFA:
- Semiconductor – PFA is awesome at protecting and delivering ultra high purity standards. It is very low leaching, creates no TOC (total oxidized carbon), and generates very few cations or anions.
- Chemical Processing – As we’ve discussed, PFAs are extraordinarily effective against corrosive chemicals and can handle extreme temperature cycling.
- Chlor-Alkali (manufacture of Cl2, HCl and Caustic) – We’re giving special mention to this subset of Chemical Processing because of its particular need to protect against a wide pH range (1-14) and aggressive oxidizing chemistry. Also, Chlor-Alkali uses electrolytic cells to produce their products. Because metals can conduct electricity, metals cannot be used in the fabrication of this equipment. But you can use non-conductive thermoplastics and dual laminate FRP equipment with a Teflon™ PFA lining.
- Pharmaceutical – Again because of PFA’s ultra high purity protection.
- Specialty Metals Processing – These companies plate and surface treat all types of metals using a specialized bath containing extremely low pH acids (e.g. Nitric, HCl, Sulfuric) to extract the valuable metals they need,
- Mining – Similar to the specialty metals processors, mining operations use sulfuric, hydrochloric and nitric acid to separate their prized metals (gold, silver, copper and nickel) from their substrates.
- Transportation Industry – To move both the pure chemicals for manufacture and the hazardous waste after processing, PFA is used to line ISO containers, storage tanks and transport vessels.
Glencore, a specialty metals processor, used to shut down its production line every 2-3 months to repair its equipment until they found a PFA lining solution offered by ECM. They haven’t had to stop production for repairs in over a year. To learn more, check out PFA Fights Acid Steam Discharge.
Teflon™ PFA vs exotic metal or glass-lined vessels
The “other” material options to fluoropolymer-lined carbon steel containers or dual laminates are containers made of exotic metal alloys or lined with glass. Each alternative presents its own challenges.
Exotic alloy metals can certainly work. But they can be very expensive, sometimes more than twice the cost of a Teflon™ PFA-lined carbon steel solution. Plus, they are plagued by availability issues. You might have to wait several months for the exotic metal component (i.e. titanium, nickel alloys) to be obtained so the alloy can be manufactured. This has even led to a standing industry joke – “Are we still waiting for the unobtainium to arrive?”
While a glass lining can work in some situations, it has its own drawbacks, including vulnerability to mechanical shock, alkaline attack, HF acid impurities, thermal stress and abrasion.