Electro Chemical Manufacturing/SDL Collaborating with MTI on New Dual Laminate Training Program
Published on: October 17, 2023 Topics: LiningsAlthough dual laminates have been around since the 1960s, finding a universally agreed upon set of best practices for incorporating these fiber reinforced plastic (FRP) thermoplastic-lined products into your tanks and piping systems is nearly impossible. In fact, the first standards for welding of plastics, including liners, were not even introduced until 2015.
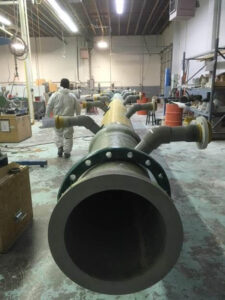
Few fabricators in North America provide dual laminate solutions for industry, and all deliver slightly different solutions. “There is a lot of history about dual laminates, but the history is based on companies developing their own standards,” according to Greg O’Brien, Vice President and General Manager at Superior Dual Laminates. “These standards have developed over time, but they’ve developed individually. Now processing industry members are asking questions like, ‘Why does one fabricator do this and another fabricator do that?”
Dual laminate systems can extend equipment life
Developing a consistent, reliable set of best practices for dual laminate systems is important. “The whole world is totally different when you are dealing with metals when compared with dual laminates,” explains O’Brien. “Dual laminates are not a miracle cure, but they are the right choice for certain chemical environments. For example, you cannot put certain chemistries with metals – 20 parts per million of chlorine will literally tear apart stainless steel in months-time. If you put a PVC-based lining material in that environment, that product will probably last a long time.”
Dual laminates, which are cost-competitive with some of the most corrosion resistant metals, are an investment that can really deliver a significant ROI by extending equipment life ─ when built and installed properly. However, with only ASME’s RTP1 for dual laminate tanks and its NM1 and NM2 for thermoplastic individual piping and FRP piping to rely on, resources are limited for projects involving dual laminate pipe, vessels, flanges and other equipment.
Developing dual laminates best practices
For decades, SDL has provided end users with dual laminate lining systems that protect fiberglass and fiberglass reinforced plastic (FRP) tanks, pipes and equipment from chemical attack, permeation and contaminants. Now the Materials Technology Institute (MTI) has asked O’Brien to help develop a Dual Laminate Training Program that will share best practices with its members worldwide.
“What we’re trying to do is get a group of experts together to give a consensus on the key points that are critical in the various aspects of dual laminates,” explains O’Brien. “For example, we’re looking at how you select the materials of construction for projects like dual laminate vessels. We are looking at how you fabricate and install materials. How do you handle them when you’re shipping and storing them? It’s really a cradle-to-grave type listing of information for dual laminate materials.”
MTI course outline
- Overview
- MOC/Materials Selection
- Design of Vessels, Piping and Flanges
- Fabrication of Dual Laminate Vessels
- Fabrication of Dual Laminate Piping
- Welding/Joining
- Installation
- Qualifying a Dual Laminate Fabricator
- Testing, Techniques and Tools
- Inspection
- In Service Inspection
- Evaluation for Service
- Repair/Alteration
- Case Histories
- Summary/Evaluation Text
“We fabricators all do different things for different areas,” points out O’Brien. “We all make flanges differently. We all make fittings differently. What this type of training does is bring to light some of those differences and what we feel are best practices. There are a lot of ways you can go about something, but if you have guidelines focusing on the major issues, you can get to the end result accurately, no matter what path you take pretty much, as long as you know those specific details that are critical to the success.”
The Dual Laminate Training Project will culminate with live or virtual training sessions. Visit mti-global.org to find out how to join MTI and participate in this and other valuable educational opportunities.