Biodiesel Industry: Fluoropolymers Replace Failed Rubber Linings
Published on: October 17, 2023 Topics: LiningsSince 2005, Electro Chemical Manufacturing (ECM) has been providing protective fluoropolymer linings for rubber liner repair projects in the biodiesel industry. Biodiesel production equipment depends on the use of corrosion-resistant materials. While many plants rely on soybeans to make this sustainable, eco-friendly fuel, an increasing number are using even more corrosive waste oil from the restaurant and food services industry as a feedstock.[1]
In biodiesel production, fatty acids from these feedstocks can corrode carbon steel and have led to degradation in the “weakest link” in some steel and even some stainless steel equipment – the welds. To combat corrosion, the industry first turned to low-cost rubber linings. In many cases, those rubber-lined tanks lasted 6 to 18 months and then failed.
In addition to containing corrosive acids (acetic, formic, hexanoic and propionic acids), the presence of solvents can accelerate degradation of many polymers and elastomers. The fatty acids present in the biodiesel cause the rubber to swell, become brittle, crack and ultimately fail.
“They were realizing in a pretty short period of time that the rubber lining was degrading,” according to Mike Bunner, President at ECM. In some cases, rubber deteriorated to the point that it would delaminate and come right off the walls.
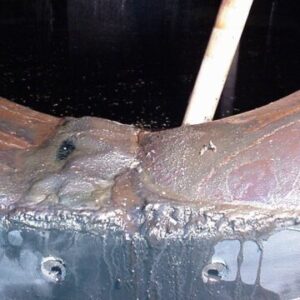
Ultimately, management teams in biodiesel plants looked for other options to avoid interrupting production for yearly elastomeric tank liner repairs, even though the upfront costs for these more reliable solutions were higher than those for an elastomeric lining alternative.
Your rubber tank lining alternative
Since 2005, ECM has been providing protective fluoropolymer linings for rubber liner repair projects in the biodiesel industry. Biodiesel production equipment depends on the use of corrosion-resistant materials. Kynar® and Halar® fluoropolymers are much longer-term solutions for rubber tank lining repair and steel vessel lining projects. Although these tank lining alternatives may cost more initially, they can last many years longer in biodiesel service. In fact, rubber lining replacement materials installed by ECM have lasted 12 – 15 years in some biodiesel tank and reactor applications.
Fluoropolymers absorb some of the fatty acids in the process but generally swell less than 10%. Kynar® and Halar® linings are considered excellent choices when it comes to long-term corrosion resistance. Both materials are able to withstand moderate temperatures (<300ºF), and ECM works with customers to determine the best fit for their needs.
Our elastomer lining repair process
Biodiesel equipment is generally shipped to ECM’s fabrication shop in Emmaus, PA, where skilled teams start the process of a rubber lining repair by removing the corroded rubber and other debris. After thoroughly cleaning and grit blasting the interior of the vessel, technicians and welders install a new homogenous lining. Fluoropolymer linings are much thicker than spray-on coatings, which may not offer equivalent corrosion resistance. In harsh chemical environments like biodiesel production, thicker linings can provide much longer protection than is available from coatings.
Kynar® and Halar® are available in thicknesses up to 1/8 of an inch, and 90 mils tends to work well for most biodiesel applications. In all rubber tank lining replacement projects, ECM also custom fits its liners through any nozzles and out over the flange faces in vessels to ensure a continuous corrosion barrier throughout the equipment.
We test liners to improve reliability
The reported defect rate for ECM linings is the lowest in the industry. The goal is to provide long-lasting elastomeric lining replacement that avoids the need for costly downtime and warranty work. ECM’s quality assurance-trained technicians spark test the repaired vessels to ensure there are no pinholes or other problems with the new protective liner. But ECM takes reliability one step further, performing a helium leak test to detect pinholes 100 times smaller than a spark tester can detect. By taking these steps, ECM provides customers with the highest quality product that they can depend on year after year.
Please contact ECM for help with any of your rubber lining repair projects in the biodiesel industry.
[1] Materials Performance (February 2019), “Equipment, Materials, and Corrosion in the Biodiesel Industry”, M. Coronado, G. Montero, C. Garcia, M. Schorr, and B. Valdez