PYROFLEX® Sheet Membrane System Protects in Corrosive Applications
Published on: September 2, 2022 Topics: Chemical ProcessingExtremely corrosive processing applications, such as those for sulfuric acid production or hydrometallurgy, require resistant interior linings on equipment to help prevent leaks and corresponding hazardous consequences, including environmental contamination or damaged equipment. Knight Material Technologies (KMT) offers its proprietary PYROFLEX® sheet membrane liner as an integral part of its system for corrosion protection in autoclaves, chemical processing vessels and equipment that require materials resistant to sulfuric acid. The liner serves an essential function as an expansion joint between the vessel’s shell and the structured brick media layer(s). Discover the features that provide superior performance for PYROFLEX compared to other types of linings and select the industry’s leading protective system for corrosive applications.
What is PYROFLEX?
PYROFLEX is a unique and proprietary protective lining system engineered for maximum durability and lasting pliability in demanding and extreme environments. PYROFLEX is compounded from a carbon base material – a corrosion-proof, thermoplastic, flexible, non-porous and durable resin. This lining can be electrostatically tested to ensure a pin-hole free, monolithic liner. In addition, it resists inorganic alkalines such as caustic soda and salts and is not affected by reducing agents.
PYROFLEX sheets fuse directly to metal and concrete surfaces, without the need for special adhesives, which can break down over time. Adjacent sheets are butted and fused together with joint strips for a continuous uniform surface with no lap joints and no need for welding.
This application, unique among acid-resistant membranes, eliminates weld or joints common to other types of sheeted liners that can weaken or crack under the pressure and thermal temperature variances and expansion common inside an autoclave. Any crack or weakness can be exploited (penetrated) by corrosive substances, causing leaks or system failure and environmental damage in addition to ruining capital equipment.

ASME Autoclave Construction Standards
Autoclaves that meet ASME standards are constructed of titanium clad steel, or a carbon steel shell, with added layers of protection from an impermeable membrane and acid-resistant brick. The layering consists of the steel shell, acid-resistant membrane, and acid-proof brick and mortar in one to three layers itself, to help reduce the temperature load on the membrane. Standard membranes are not always applicable to autoclaves because of the high operating temperature. Here is where PYROFLEX is a clear choice because of highly resistant to thermal decomposition as compared to other acid-resistant membranes, especially those that use adhesives to bond to the shell.
The Importance of Viscoelasticity in a Thermal Liner
Under wet acidic conditions, bricks swell adding stress to the liner. More stress is added from high temperatures and thermal expansion differentials between steel and brick.
Steel and brick, while both hard substances, expand at different rates, with the thermal expansion of steel two to three times higher than brick. The viscoelastic properties of PYROFLEX lend it the ability to soften, remaining pliable during thermal expansion events throughout its lifespan. This gives PYROFLEX the ability to act as an expansion joint between the bricks and the steel shell.
When selecting the lining for an autoclave, factors include:
- Thermal properties of the brick and mortar
- The number and thickness of brick layer(s)
- Operating pressure and temperature
- Expansion of brick and steel
This characteristic of viscoelasticity alone helps PYROFLEX outperform traditional asphaltic and fiber-reinforced resin alternative linings, which become porous and cracked. In addition, the typical liner thickness of PYROFLEX is six to nine millimeters, compared to other alternatives that can be as thin as three millimeters.
In other characteristics, PYROFLEX does not experience thermal decomposition at temperatures under 500° F. With protection of courses of acid resistant bricks on top of PYROFLEX, our brick lining system can operate at temperatures as high as 2300° F. While the PYROFLEX membrane does not sag at 300° F, normal practice attempts to limit the sheet lining temperature to 250° F with the projection of brick layers of PYROFLEX membrane.
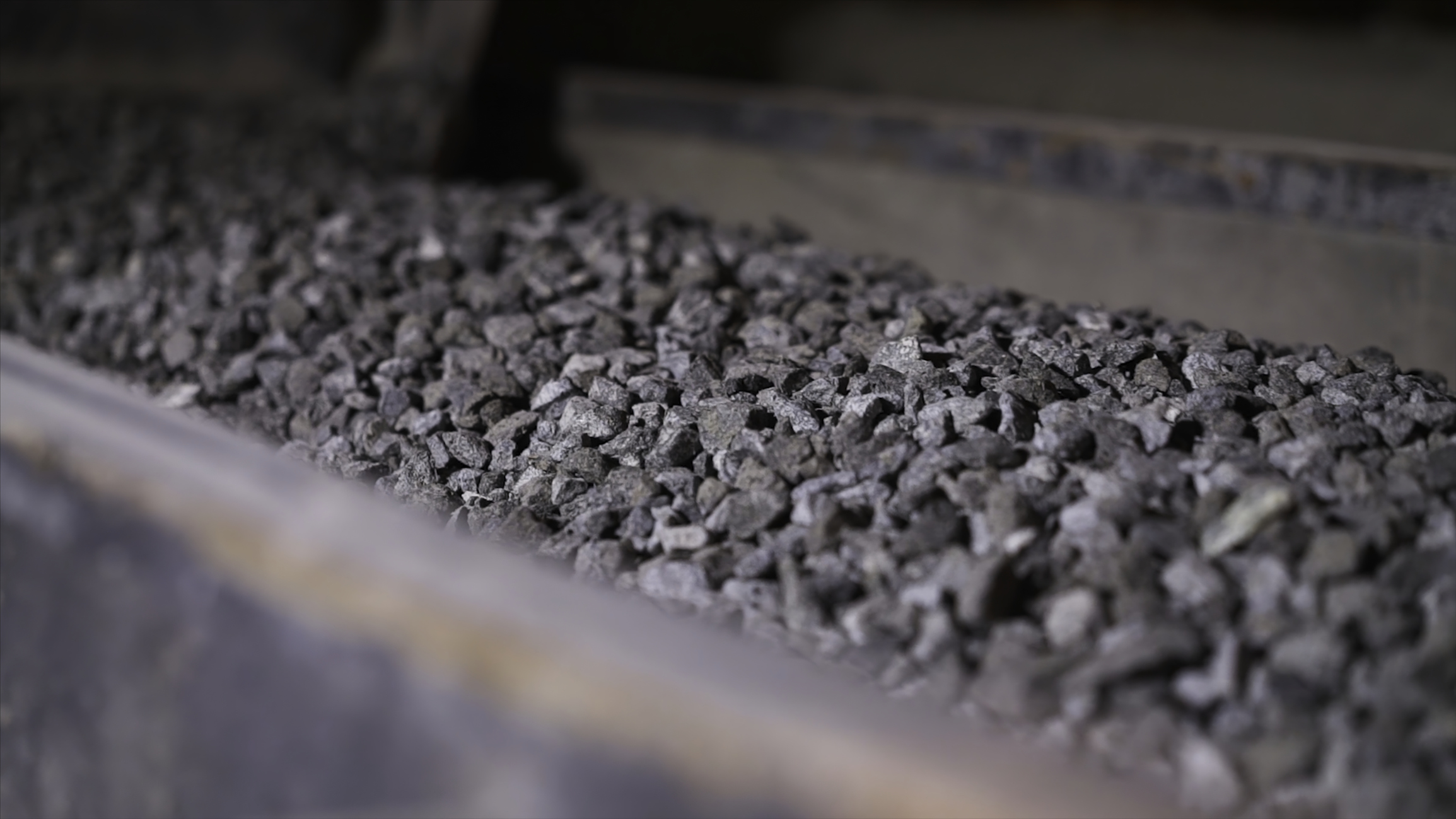
Repair Potential as Part of Continuing Maintenance
Maximizing cost efficiency and production uptime, PYROFLEX can be quickly repaired if needed. Sections can be repaired without compromising the structure of the entire lining, unlike other acid-resistant membranes, which must be replaced in their entirety when damaged. A special heating process mates the new section of the lining around it, creating a seamless and long-lasting patch to extend service life without disrupting production processes.
Improve the Operational Function of Your Autoclave
Hydrometallurgical processing relies on autoclaves to yield metals such as gold, nickel or zinc. In former times, a smelting process was required, however, the downsides of smelting are many, including high energy consumption and toxic pollutant residue.
Autoclaves modernize this process but come with the added stress of higher temperatures and pressures. This, in turn, demands technologically advanced liners and autoclaves for processing. KMT PYROFLEX liners and brick lining systems lead the industry for protective linings that offer durability, reliability and energy savings. PYROFLEX is a cost-effective option when considering the mitigation of unplanned downtime or possible environmental hazards that can arise during the hydrometallurgy process.
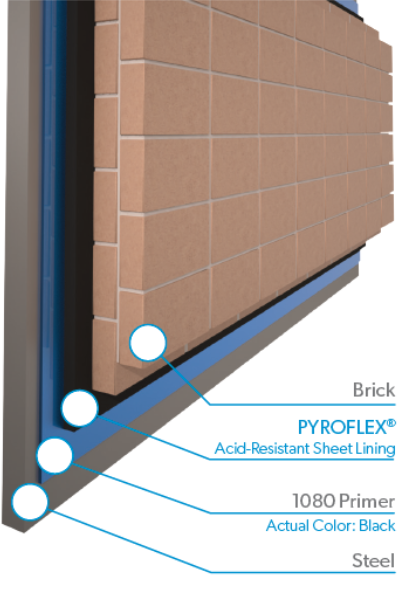
Superior High Heat and Acid Resistant Sealant
PYROFLEX is part of a complete solution for any system with a high heat or acidic environment and is not limited to autoclaves. It also supplies protection within a lining system incorporating acid-proof bricks and mortar in pre-heater tanks, flash vessels, neutralization tanks, secondary containment and more. In fact, there are sulfuric acid vessels in service for 40 years and more that rely on lining systems from Knight that incorporate PYROFLEX for protection.
Additional Lining Options – Fluoropolymer Linings and Coatings
In addition to PYROFLEX by KMT, our subsidiary, Electro Chemical Manufacturing, offers another type of solution for acidic environments, fluoropolymers linings. Fluoropolymers serve as a stand-alone lining option with long-lasting and ultra-pure characteristics. Choices in fluoropolymer linings for steel-lined vessels include PFA, PTFE, FEP and more. If you want to learn more, visit Electrochemical.net for the range of fluoropolymer linings available.
More About Knight Materials
PYROFLEX lining and complete corrosion protection systems, including acid-proof bricks and mortar, are available from KMT for existing and new projects. As a corrosion engineering company, KMT not only manufactures heat and acid-resistant materials, but also engineering and installation services. Contact us today about your next autoclave or chemical processing project.