How the Switch to Structured Media Cuts Down on Repacks, Energy Costs and Unplanned Shutdowns
Published on: December 5, 2024 Topics: FLEXERAMIC ®, Heat Transfer Media, Thermal DestructionRegenerative Thermal Oxidizers (RTOs) are vital in reducing industrial air pollution through the thermal destruction of volatile organic compounds (VOCs) and hazardous air pollutants (HAPs). As industries face growing pressure to optimize operations in response to tightening environmental regulations and fluctuating energy costs, enhancing the efficiency of RTOs has become a priority. One key optimization strategy lies in choosing the right ceramic packing media. This guide explores how structured ceramic media, like FLEXERAMIC® from Knight Material Technologies, can improve energy efficiency, reduce operational costs, and extend uptime by reducing repacking and maintenance needs.
Priorities driving RTO optimization
RTOs are favored for VOC and HAP abatement due to their energy recovery capabilities and continuous operation without cool-down periods. However, a variety of industry priorities are pushing RTO manufacturers to improve their operating efficiencies:
- Increasing energy costs are adding a sense of urgency to RTO improvements. One factor that can help is the packing media used in the RTO. Pressure drop and media fouling can diminish energy savings, leading to higher operating costs. By strategically selecting packing media, companies can mitigate these issues, reduce repacking frequency and avoid fines for environmental non-compliance.
- Stringent environmental regulations are pushing industries like fiberglass, pulp and paper, paint and cement to improve RTO efficiency.
- Manufacturers are constantly seeking ways maximize uptime by minimizing unplanned shutdowns due to repacks. In industries like automotive manufacturing, downtime can cost as much as $50,000 per minute, or even more, making reliable RTO operation crucial.
Structured packing vs. random packing media for RTOs
Structured packing, such as the corrugated FLEXERAMIC structured media, offers several advantages compared to random packing, like ceramic saddles. One example is that random packing is prone to uneven gas distribution and deposit buildup, causing hot spots and clogging. In contrast, FLEXERAMIC’s engineered design ensures uniform gas flow and minimizes fouling. Its corrugated structure increases surface area and turbulence, promoting better particulate disengagement and reducing pressure drop, leading to extended service intervals and lower maintenance costs.
Benefits of FLEXERAMIC structured media
FLEXERAMIC structured packing provides substantial improvements in energy efficiency and operational performance compared to traditional ceramic saddles:
- Lower pressure drop: FLEXERAMIC’s design reduces pressure drop by 35%, meaning fans and blowers require less energy to move process air, directly cutting energy consumption.
- Improved gas distribution: The structured media ensures even gas flow, preventing localized buildup of deposits and promoting efficient heat transfer.
- Compact bed design: FLEXERAMIC’s efficient design allows for reduced bed depth, enabling a smaller RTO footprint while maintaining high operational capacity.
- Extended lifespan: The media resists fouling and clogging, resulting in longer intervals between replacements. This minimizes downtime and reduces repacking costs, providing long-term savings.
- Lower capital and operating expenses: With its higher efficiency, FLEXERAMIC allows companies to install smaller, more cost-effective RTO units. Additionally, the accumulated energy savings over time often offset the installation cost within a year.
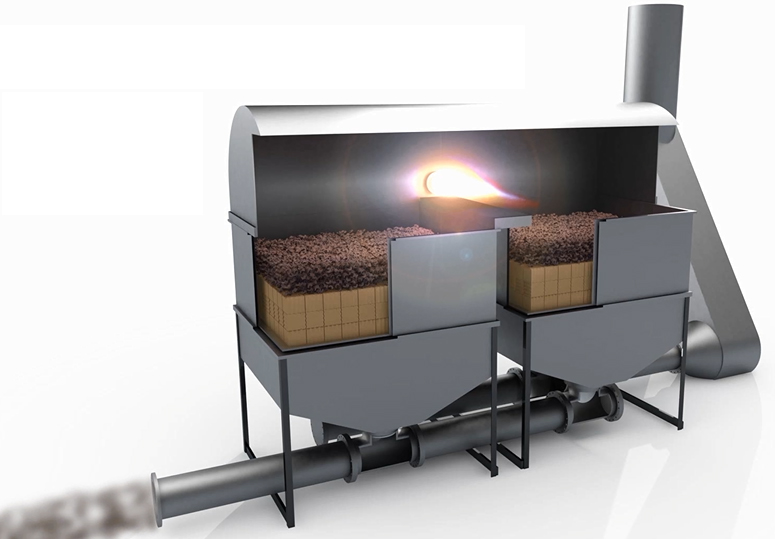
Real-world case studies of savings from FLEXERAMIC structured media
The switch to structured ceramic media in regenerative thermal oxidizers (RTOs) has delivered significant operational and financial benefits across various industries. Several real-world examples highlight the impact of this switch that demonstrate the impressive cost reductions and efficiency gains achieved by adopting structured media:
- Fiberglass manufacturing: A major U.S. fiberglass producer switched to FLEXERAMIC media, which extended the RTO’s media lifespan from 3-6 months to 2-3 years. This reduced downtime for repacking from 4-5 days every few months to 2-3 days every few years.
- Packaging industry: In a southeastern U.S. packaging company, FLEXERAMIC reduced energy costs by 25% compared to traditional ceramic saddles. The structured media’s lower pressure drop reduced the total energy expenditure by more than $1 million annually.
- Paint operation: A southern U.S. paint operation saw a 50% reduction in energy costs after switching to FLEXERAMIC media. The facility saved more than $100,000 annually in electricity costs, thanks to a 60% lower pressure drop than ceramic saddles.
- Wood products manufacturer: A wood products facility saved nearly $500,000 annually after switching to FLEXERAMIC, cutting energy costs and reducing pressure drop by 50%.
Structured Media for Long-Term Savings
Switching to structured ceramic media like FLEXERAMIC in RTOs can significantly reduce energy costs, maintenance frequency and unplanned shutdowns. These real-world examples highlight how structured media improves efficiency, enhances sustainability and boosts profitability. For industries facing rising energy costs and tightening regulations, investing in structured media is a strategic move that provides immediate and long-term benefits.
Read the full Regenerative Thermal Oxidizer Efficiency Guide to learn how to cut down on repacks, energy costs and unplanned shutdowns.