Advanced Tower Internals: Engineered Solutions for Aggressive Chemical Processing Environments
Published on: April 10, 2025 Topics: Chemical ProcessingChemical processing towers face an ongoing battle against corrosion, temperature extremes and mechanical stress—particularly in aggressive chemical processing environments such as towers devoted to sulphuric acid. Traditional materials fail prematurely, causing unscheduled operational shutdowns or frequent maintenance for repair and replacement, excess replacement costs and potential safety hazards.
A strategic collaboration between sister companies Superior Dual Laminate Products (SDL) and Knight Material Technologies (KMT) gives processors access to tower internals that leverage each company’s expertise: SDL as an industry leader for high-performance thermoplastics and dual laminates combined with KMT’s globally recognized leadership in tower capabilities for engineering, design and corrosion resistant media.
Custom-engineered internal components not only optimize mass transfer efficiency but also provide superior chemical resistance and mechanical stability, extending service life to 8-15 years even in the most challenging operating conditions.
Advanced Dual Laminates Materials Technology
SDL tower internals leverage state-of-the-art thermoplastic and composite materials, including CPVC, PVDF, PFA and FRP (fiberglass-reinforced plastic). This diverse materials portfolio optimizes component design for specific process conditions, with temperature resistance up to 210°F (100°C). SDL’s dual-laminate construction techniques combine thermoplastic liners’ superior acid resistance with FRP’s structural advantages, ensuring long-term reliability for an anticipated life expectancy of 8-15 years in aggressive chemical environments. Materials are carefully matched to process requirements.
Comprehensive Component Portfolio
- SDL manufactures a complete range of tower internals designed to support packing media within tanks:
- Gas distribution support plates
- Liquid redistributors
- Self-supporting dome packing supports
- Bar supports and internal beams
- Internal feed pipes
- Custom FRP fastening systems
The superior manufacturing capabilities for dual laminate internals accommodate structures up to 12 feet in diameter, with designs optimized for installation through standard manways (usually 24-30 inches) or body flanges.
Engineering Excellence
The engineering approach combines decades of materials experience with rigorous analysis of process requirements. Each application presents unique challenges requiring careful consideration of multiple variables. A comprehensive view of system requirements and operational conditions ensures optimal component design and material selection. Every internal component is engineered for optimal performance, considering critical factors such as:
- Process temperature and pressure requirements
- Chemical compatibility and corrosion resistance
- Flow distribution characteristics
- Mechanical loading and flex modulus
- Thermal expansion coefficients
- Vacuum service capability
This meticulous engineering application-specific approach ensures that each component meets the highest standards of performance, durability and reliability. By integrating advanced materials expertise with a deep understanding of process conditions, the design process optimizes functionality while minimizing risks.
Quality Assurance
Quality isn’t just a checkpoint in our process but fundamental to every step of construction. From material selection through final inspection, every step of our manufacturing process adheres to rigorous industry standards and internal quality protocols. Our quality program incorporates:
- ISO 9001:2015 certification
- Fabrication to ASTM C1147 specifications
- Welding per ASME G110 standards
- Regular third-party weld testing
- Comprehensive quality control protocols
- Long-tenured staff with extensive material expertise
- Cost-effective solutions through vertical integration
- Rapid response to custom requirements
The result of SDL quality assurance results in repeat customers, an exact fit and an extended lifespan. By adhering to strict certifications, rigorous testing, and comprehensive quality control protocols, solutions that exceed customer expectations. With an experienced team, advanced fabrication techniques, and a vertically integrated process, the design team provide cost-effective, high-quality products while maintaining flexibility to respond quickly to custom requirements.
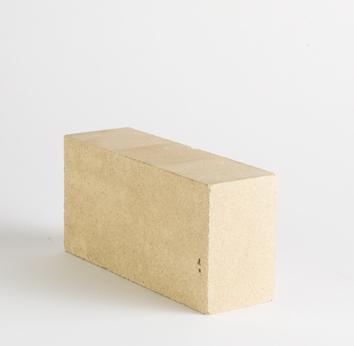
Applications
Tower internals are engineered to meet the demands of the most challenging chemical processing environments. Through careful material selection and design optimization, solutions excel in applications where traditional materials fall short. Whether managing aggressive chemicals or maintaining precise process conditions, our components provide reliable performance in demanding applications, including:
- Caustic scrubbers
- Chlorine dryers
- Chemical processing equipment
- Industrial gas handling systems
- Corrosive media processing
Combining KMT’s acid-resistant ceramic media and tower engineering expertise with SDL’s thermoplastic internals provides the simplicity of a single-supplier solution for tower protection systems. This integrated approach for chemical processing facilities eliminates interface compatibility issues and streamlines design specifications while ensuring optimal resistance in harsh environments throughout the entire tower structure.
Need a complete tower protection solution? Contact our engineering team to develop specifications that address both your ceramic lining and internal component requirements, maximizing service life and minimizing operational risk.