Choosing the Right Ceramic Media for Regenerative Thermal Oxidizing Towers
Published on: March 31, 2023 Topics: FLEXERAMIC ®, RTOCompare and Contrast FLEXERAMIC® to Monolithic
Many industries require a regenerative thermal oxidizing (RTO) tower to remove volatile organic compounds (VOCs) to meet environmental compliance standards. The ceramic heat transfer media within the tower acts as an essential element to enable efficient operations. The best tower build or retrofit enables “set it and forget it” operations—requiring little maintenance while supplying trouble-free performance for years to come.
Whether planning a retrofit, an upgrade or a new construction project, there are three basic choices for ceramic heat transfer media to pack inside the tower to capture volatile organic compounds (VOCs), random saddle media, monolithic blocks or FLEXERAMIC® structured packing from Knight Technologies. All have their pros and cons, so how to choose the right type of media for your tower operations? Comparing and contrasting the three main types, random, monolithic and FLEXERAMIC structured packing, can help pinpoint the best choice.
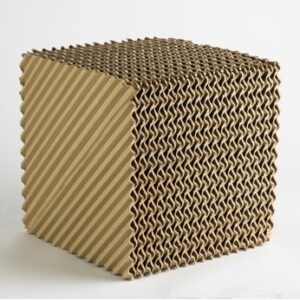
FLEXERAMIC structured media for heat transfer
How does a regenerative thermal oxidizer work?
The regenerative thermal oxidizer (RTO) tower controls VOCs, hazardous air pollutants (HAPs) or other gases emitted through various industrial processes, using combustion to convert these emissions into more harmless carbon dioxide and water vapor prior to their exhaust. Generally, any industry that relies on organic solvents or chemicals that can release VOCs or HAPs must use an RTO to achieve environmental compliance. Types of industries that commonly rely on RTOs to handle emissions can include manufacturing and processing, paints and coatings, and some pharmaceuticals, among others.
These towers are packed with ceramic or heat transfer media, supplying a critical design component. The ceramic media acts as a heat exchanger, transferring heat from the combustion chamber to the incoming exhaust stream. This helps raise the exhaust gas temperature to the point where the VOCs can be oxidized and converted to carbon dioxide and water. One key element to finding the right ceramic material is choosing one that can withstand high temperatures and is an effective thermal storage medium, meaning it can hold heat for a long time.
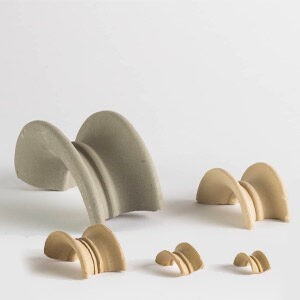
Random heat transfer media
What is random packing vs. structured packing?
The ceramic media inside the RTO can be arranged in all random packing, structured packing, or in a combination of random and structured packing. Random packing refers to ceramic media saddles or smaller ceramic parts placed in a layer or layers within the RTO chamber in a random manner. This type of ceramic media can serve smaller RTOs, where the cost and complexity of structured packing aren’t needed, or it can serve as a layer of packing media in addition to structured layers. Either way, the ceramic media forms a bed for heat transfer that the exhaust gases pass through as they travel through the RTO.
Structured packing for a regenerative thermal oxidizer involves a configuration where ceramic media blocks are arranged in a specific pattern. The number of blocks and their arrangement is determined by the applications engineers, who look at parameters including thermal efficiency, pressure drop, gas distribution and the characteristics of the particulates that pass through. This examination of the type of particulates includes the level of contamination or dirt in the gas stream to calculate how soon the media bed might plug. The advantage of structured packing is that it provides a more uniform and predictable flow through the RTO, which can reduce pressure drop and improve system efficiency.
The amount of pressure drop measures the resistance of the fluid or gas to flow through a system and is one of the more important considerations in RTO design and operation. The higher the pressure drop from one area to another; the more energy is needed to force the air through the ceramic media. Lower pressure drop translates into reduced energy consumption over the lifespan of the equipment for more manageable operating costs and overall system efficiency. The lower the pressure drop, the less pressure on RTO components such as fans, motors, and ductwork. The pressure drop can be predicted and controlled by optimizing the size and configuration of the ceramic media inside the RTO, in addition to selecting the appropriate type and size of fans and ductwork.
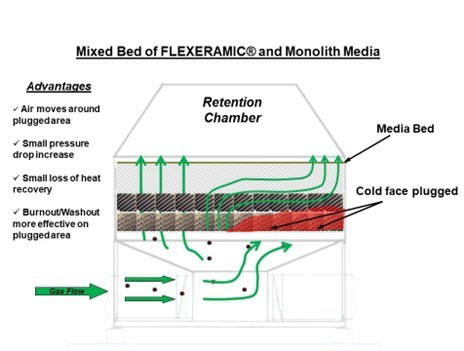
Structure heat transfer media has continuous airflow, even around plugged areas
The difference between monolithic and FLEXERAMIC structured packing
Both monolithic and FLEXERAMIC structured packing are used in an RTO to treat air pollutants but differ in terms of design and performance characteristics.
Monolithic ceramic media is a solid block with numerous parallel channels or passages that run the length of the block. The channels allow the air or gas to pass straight up through the media, with the ceramic surface area allowing contact between the air or gas and the catalyst.
On the other hand, the FLEXERAMIC structured packing features a proprietary corrugated pattern that creates a series of angles channels or passages instead of a straight line found in monolithic media. The corrugated design supplies different benefits, creating a greater surface area per volume unit. This results in more efficient VOC or pollutant removal and more efficient heat transfer than an equivalent amount of random saddle packing or monolithic media to reduce bed depth. Other benefits from this design include:
- Minimizes channeling
- Radially distributes gas and liquid
- Supplies greater resistance to fouling than random or monolithic media
- Increased flow and lowers pressure drop
These factors can lead to a reduced footprint for a new build design. This not only reduces construction costs but also means lower energy consumption and reduced utility costs during the lifetime of the RTO with more efficient pollutant removal. In addition, it is less subject to fouling or blockage compared to monolithic, and it can more effectively treat larger volumes of air.
Due to fouling or blockage, the monolithic media can require more frequent maintenance than FLEXERAMIC structured packing. For heat transfer and mass transfer applications, the flow characteristics that result from the geometrical arrangement of the FLEXERAMIC structured packing blocks create a highly effective surface area, resulting in good efficiency compared to other heat transfer media.
Often the best combination involves a bed that combines the two types. Should the monolithic media experience cold face plugging, a tower design incorporating monolithic media with a bed of FLEXERAMIC structured packing above it will result in air movement around the plugged area. A small pressure drop increase that does not contribute significantly to energy costs, a small loss of heat recovery, and a burnout/washout more effective on the plugged area.
Our application engineers are available to work with your project to draw up the optimal design for your specific application to maximize RTO performance. Achieve environmental compliance, create a safer workspace, reduce energy costs and maintenance issues, and achieve target performance for your RTO retrofit or new build with the right ceramic media and tower design from Knight Material Technologies. Contact us to start your consultation.