Structured Packing vs Random Packing for RTOs
Published on: June 29, 2023 Topics: Random Packing, RTO, Structured PackingRegenerative thermal oxidizing towers (RTOs) depend on the ceramic media within to optimize the tower’s performance and efficiency. The selection of ceramic media type can make a significant difference throughout the lifespan of the RTO in terms of time and costs. There are differences and nuances among ceramic media choices. Understanding these differences can help operators and plant managers make a well-informed decision that helps reach target goals for pollutant removal and air quality control while cutting maintenance time and sparing energy expenditures.
FLEXERAMIC® structured packing and random packing are commonly used in RTOs (Regenerative Thermal Oxidizers). The use of packing facilitates the transfer of heat between the exhaust gases and the incoming air streams. A vital component of any RTO is using proper heat transfer media to mitigate potential problems while ensuring reliable, economical and safe operation.
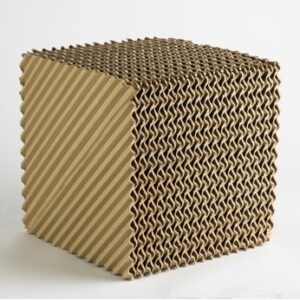
Comparing the differences between FLEXERAMIC structured packing and ceramic random packing
In planning a rebuild or an original design, engineers can use a mix of random ceramic saddles and structured packing, all random packing or all structured packing. Keep in mind there are critical differences between these two packing materials that make FLEXERAMIC structured packing available from Knight Material Technologies a more attractive option.
Here are some benefits of using FLEXERAMIC structured packing over random packing in an RTO:
- Improved transfer efficiency: FLEXERAMIC structured packing has a higher surface area per unit volume than random packing, improving the RTO’s flow efficiency. Higher flow efficiency means more pollutants can be removed from the exhaust gases with less energy consumption.
- Reduced pressure drop: FLEXERAMIC structured packing has a lower pressure drop than random packing, requiring less energy to push the gases through the RTO. This can lower operating costs and save energy.
- Increased resistance to fouling: FLEXERAMIC structured packing is less prone to fouling than random packing. Fouling occurs when particulate matter or other contaminants build up on the surface of the packing material, reducing its effectiveness. FLEXERAMIC structured packing has a more open structure that allows contaminants to pass through more efficiently, reducing the risk of fouling.Cleaning packing in place is nearly impossible and usually very ineffective. Companies can avoid unnecessary or excessive downtime devoted to cleaning the ceramic packing with the proper selection of the right style ceramic packing that best suits the application. In some cases, the best design option will include a mixture of structured and random packing.
- Improved durability: FLEXERAMIC structured packing is made from high-quality random packing that is highly resistant to corrosion and thermal shock. This makes it a more durable option than random packing, which can be more susceptible to damage and wear over time.
- Less room in bed height: Since FLEXERAMIC structured packing is more efficient, designs can call for less bed height. The bed height requirement can be figured into the cost-efficiency of the initial build and rebuilds.
- Increased heat transfer: FLEXERAMIC structured packing is designed to maximize surface area, facilitating heat transfer efficiency. The uniform flow distribution creates turbulent flow conditions vs. the irregular flow patterns common to random packing.Improved heat transfer enables waste gas hydrocarbons to ignite on their own. This increases the system’s efficiency and creates a temperature rise that furthers the burn of waste gases. Reaching a temperature threshold via improved heat transfer can help reduce fuel consumption to further aid in energy conservation.
- Higher resistance to chemical attacks: FLEXERAMIC structured packing has a unique glaze layer that helps increase resistance to withstand attacks from acids, bases and organic solvents in corrosive environments.In addition, FLEXERAMIC structured packing has a higher rate of ALUMINA (AL203) than random packing (34% vs. 10-28%, depending on the make-up), which accounts for hardness and stable crystalline structure. The higher rate allows FLERAMIC structured packing to withstand higher chemical levels without degradation or damage.
The difference between structured packing and random packing comes down to the increased surface area that provides efficiency in pressure drop, heat transfer and resistance to fouling.
Structured packing vs. random packing data
Let’s look at the data differences between FLEXERAMIC structured packing and random packing as tested by an independent lab. The test conditions were based on two 8′ deep beds with 70°F inlet, 1500°F combustion, and 180-second switch time. The fuel is natural gas with 0% excess combustion air added.
Thermal Energy Recovery Efficiency* | |||||
---|---|---|---|---|---|
150 SCFM/FT2 | 200 SCFM/FT2 | 250 SCFM/FT2 | 300 SCFM/FT2 | 350 SCFM/FT2 | |
FLEXERAMIC® 28 Structured Packing | 95.54% | 95.12% | 94.77% | 94.46% | 94.19% |
Ceramic Random Media | ~93.5% | ~92.8% | ~92.3% | ~91.9% | ~91.5% |
*Recommended efficiency is 95% and above
Pressure Drop (inches wc through inlet and outlet beds) | |||||
---|---|---|---|---|---|
150 SCFM/FT2 | 200 SCFM/FT2 | 250 SCFM/FT2 | 300 SCFM/FT2 | 350 SCFM/FT2 | |
FLEXERAMIC® 28 Structured Packing | 3.8″ | 6.8″ | 10.6″ | 15.3″ | 20.9″ |
Ceramic Random Media | ~5.3″ | ~9.45″ | ~13″ | ~21.35″ | ~29.15″ |
Cost-benefit of structured packing vs. random packing
Overall, structured packing is better than random packing at meeting trends for RTOs to move to efficiency, energy consumption and regulation compliance since the design that begins with structured media will meet the operational objectives and provide more prolonged operational use. All of these differences should be considered when designing or rebuilding an RTO.
Start your engineering consultation with a sales engineer
Do you want to talk about the latest RTO packing material technology for a refurbishment or new installation? The engineering staff at Knight Material Technologies can support your next project from conception through completion and help design the packing for your application. Improve your RTO performance with a call to Knight today. For more information on FLEXERAMIC structured packing, see the brochure.