Kynar® PVDF – A Versatile, Effective and Economical Fluoropolymer Lining
Published on: October 17, 2023 Topics: LiningsOf the fluoropolymer linings available, PVDF (Polyvinylidene Fluoride) is the most commonly used. And with good reason.
PVDF offers excellent chemical corrosion and permeation protection in a wide variety of applications. It’s very effective against chlorinated and brominated solvents. It’s very malleable and easily shaped. When bound to a substrate, depending on the chemicals involved, it’s thermally stable in temperatures up to 230°F. It comes in a range of sheets and resins and is significantly less costly than other fluoropolymers or exotic metal alloys.
Because of its versatility and affordability, PVDF has found a home in almost every chemical, pharmaceutical and semiconductor facility in the world. With multiple grades available, whether your system requires high abrasion resistance, high stress crack resistance or protection from extreme cold, PVDF can service your needs in a cost-effective manner.
As the chart below shows, fluoropolymer linings overall hit the financial sweet spot for both capital and operating expenses when compared to carbon steel and exotic metal alloys in preventing chemical corrosion and permeation.
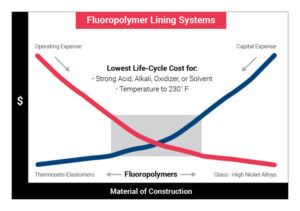
But, when researching fluoropolymer lining options, many people overlook that there are 6 classes of fluoropolymers to consider. They often default to asking for a bid for Teflon® as their lining.
Teflon® is an awesome lining and provides outstanding protection against very challenging chemical corrosion and permeation. However, many other fluoropolymers provide excellent protection as well. The smartest choice is guided by the chemicals and reactions taking place in each situation.
That’s why it’s critical to work with a fluoropolymer lining company that knows the full breadth of lining choices available and can guide you to the most effective and economical choice that serves your needs.
At Electro Chemical Manufacturing (ECM), when we need PVDF, we work with Kynar® PVDF, made by Arkema. Kynar® PVDF is a world-recognized PVDF and serves our clients very reliably. And Arkema provides Kynar® PVDF in three different grades. If you’d like to learn about the technical specifications of Kynar® PVDF, please visit Arkema — Overview of Kynar® PVDF Products.
Kynar® PVDF works well with both steel and dual laminate equipment and tanks. It also offers superior resistance to abrasion, which matters if you’re working with slurries or other solutions with particulates.
The Kynar® resin is also used for coatings as well as liners, making this fluoropolymer useful to protect smaller equipment, complicated-shaped pieces, pipes, and tanks. Because the application process requires extreme heat to “bake” the coating to the substrate, Kynar® coatings are only applied to pieces made of carbon steel and metals that can withstand the application process. To learn more, please visit our Kynar® Coatings page.
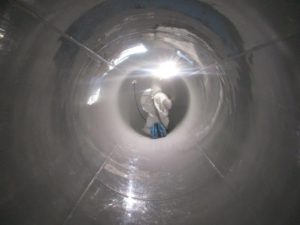
Fluoropolymer Sheet Lining
The ease with which Kynar® PVDF can be applied makes it a terrific product for field installation and repair. Oftentimes, manufacturing facilities cannot afford the downtime to take their tanks and equipment offline, disassemble them, and ship them out for refurbishment. So when the manufacturer’s chemical process supports Kynar® PVDF as a lining choice, ECM is able to do the work at the client’s location, saving both time and money.
Let’s take a look at the wide range of industries that can benefit from a Kynar® PVDF fluoropolymer liner protecting their equipment and tanks from chemical corrosion and permeation.
- Paper and pulp
- Semiconductor/chip manufacturing
- Chemical processing
- Food processing (PVDF is approved as safe by the FDA)
- Utility and power generation
- Wastewater treatment plants
- Pesticide manufacturing
- Pharmaceutical manufacturing
As you might imagine, the applications within these and other industries go on and on. Kynar® PVDF is incredibly versatile.
And, as noted earlier, when you need to protect uniquely shaped equipment like agitators, mixers, and blenders, a Kynar® coating can be an excellent choice. Of course, the geometry of the piece must allow the coating to reach all internal surfaces and corners, or the coating process will leave flaws.
To sum up, Kynar® PVDF works well in a wide variety of applications and delivers excellent performance at a very good price point.
You can learn more about the technical aspects and use of Kynar® PVDF in fighting chemical corrosion and permeation by visiting these web pages –