Boost Functionality and Performance of Your RTO While Saving on Energy Costs
Published on: June 9, 2022 Topics: RTOIncrease efficiencies, reduce energy costs and avoid unplanned shutdowns by making the right choice of ceramic media in your regenerative thermal oxidizing (RTO) towers. Both random and structured media from Knight Material Technologies supply the industry’s most effective engineered design to absorb heat, ensure low pressure drop and avoid plugging.
Knight’s proprietary design for its FLEXERAMIC® structured media offers operators distinct advantages over other styles of ceramic media for higher thermal efficiencies and the best gas distribution. The design and resulting flow help reduce energy costs to save operating expenses year over year during the decades-long lifespan common to RTOs. Discover how Knight’s advantages add up over years of RTO operation while helping prevent problems that can occur due to an inefficient media bed.
The Role of Ceramic Media in an RTO
A regenerative thermal oxidizing tower relies on thermal combustion to destroy or eliminate volatile organic compounds (VOCs) from industrial process emissions. RTOs are commonly employed to clean up the air stream from a production facility that emits relatively low levels of volatile organic compounds (VOCs), but enough to fall within EPA jurisdiction. A properly functioning RTOs can eliminate up to 99% of the VOCs emitted by a factory or production facility, creating CO2 and water as byproducts.
Ceramic media beds contribute to this air pollution control system by capturing and maintaining the heat necessary to eliminate the VOCs from the industrial exhaust. Energy expenditures occur as the RTO pushes or causes the air to flow around the ceramic media.
Performance keys for ceramic media include thermal efficiencies, with the operator looking at the thermal energy recovery (TER) estimates for a packed media bed, and the pressure drop. The pressure drop equates to the cost to move the gas. The higher the pressure drop, the higher the electric and energy usage to push or pull the gas through. The higher the TER, the lower the gas and energy usage.
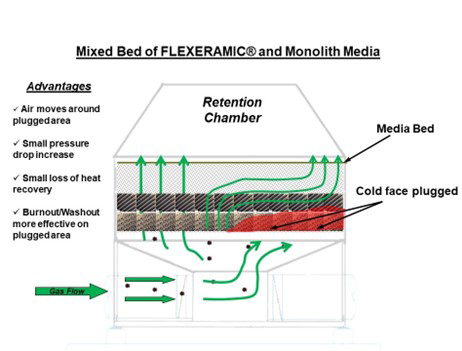
Potential Problems Caused by Inefficient or Failing Ceramic Media
The term “flows” is also key when it comes to ceramic media. Most often, if the air flow is plugged up or slows down, it is due to ceramic media bed failure or inefficiencies to correctly distribute air flow.
The available surface area and the design of the ceramic media impact performance. Potential problems that can arise due to the media bed includes plugging, which leads to higher energy costs and lower efficiencies, or worse yet, a forced shutdown.
When an RTO needs maintenance or is inoperative, some companies are required to shut down if they cannot treat their air emissions. Any facility operator knows each hour of a plant shutdown is a costly, painful event.
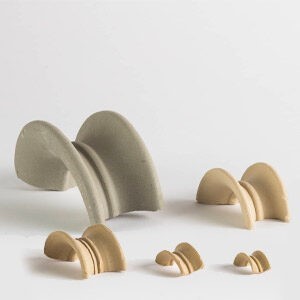
Differences Between Random and Structured Media
Ceramic media is available in a variety of shapes and sizes typically classified as either random media or structured.
Knight Materials Technologies offers FLEXISADDLE® random media and FLEXERAMIC® structured media.
The original benchmark for RTOs was the saddle random media. Knight Materials Technologies has designed its random media saddle with a greater amount of void space. This enables packing of fewer pieces per cubic foot. The LPD® ceramic random media has a high open area and aerodynamic design that results in a 20% lower pressure drop and up to 40% reduced particulate retention over standard saddle media.
The additional void space was designed in response to the presence of particulates in the exhaust streams and the never-ending challenge of particle accumulation in the RTO. The voids engineered for Knight random media will not plug as quickly as other types of random ceramic saddle media. This allows operations to proceed for longer periods of time in between maintenance to clear a plugged media bed.
The FLEXERAMIC® structured media block features geometrically arranged corrugated sheets designed to expose the greatest amount of surface area for increased thermal efficiency. In addition, the design angles the gas distribution or flow compared to a monolithic design, which relies on straight channels.
The proprietary FLEXERAMIC design offers operators several advantages:
- Greater surface area – the patented design flutes and curves on an angle through the media block for greater surface area. The greater the surface area, the more efficient the TER.
- Heat distribution – heat distribution is directly related to gas distribution for a more effective heat distribution in a FLEXERAMIC structured media bed.
- Lower pressure drop – the lower the pressure drop, the less work the fans and blowers will have to work to push the gas through the system.
- Capex – The better or more efficient the TER, the fewer layers of ceramic media required for the initial RTO design. The RTO can be smaller or shorter yet equally as efficient as a larger unit, to help save on initial capital expenses.
- Opex – Year over year as the RTO continues through its anticipated decades long lifespan, the energy savings documented for the Flex FLEXERAMIC ceramic design add up significantly.
- Sustainability – Energy efficiencies help companies reach sustainability goals
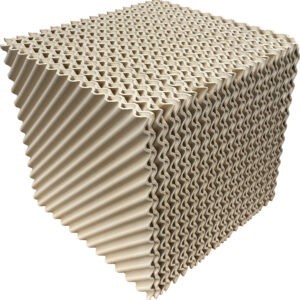
Mixed Bed or Individual Use?
Both random and structured media can be used individually or in combination in a mixed bed. Typical industries that rely on packed ceramic media can include pulp and paper, automotive finishing and painting operations or wastewater facilities.
Mixed beds are often used in the wood products industry, due to the particulate matter contained in its exhaust stream. The structured blocks packed into a bed in the bottom layers of the RTO can better capture particulates contained in the exhaust, with layers of random media atop the structured layers to offer a savings on capital expenditure.
It might be time to clean and/or repack the ceramic media bed inside an existing RTO due to diminished performance, plugging or higher energy costs. Or perhaps a facility is installing a new RTO. Contact us to ask about options for ceramic media beds and the long-term value of installing Knight Materials Technologies FLEXISADDLE® random media or FLEXERAMIC® structured media for your project.